 | WHAT MAKES THE CECONET PROCESS INTERESTING | |
All heat generators: hot water or superheated boilers, steam boilers, reheating furnaces for fluids using liquid or solid fossil fuels containing sulfur are subject to risks of low temperature acid corrosion as soon as certain conditions for the temperature and hygrometry of the fumes are put together.
It is mainly during long-lasting stoppages that these risks are greatest but acid corrosion can also happen when the generators are running.
Night or week-end stoppages, leaks on soot removal equipment, water in the soot removal fluids (steam or compressed air), unwanted air entries in the fume course, the water temperature too low or cleanings with plain water too frequent are all aggravating factors.
The interest presented by the CECONET process coupling a scaling & neutralizing chemical product with a mechanical way to eliminate residual deposits is therefore the only existing means to : - greatly reduce or even totally eliminate the use of water, the most commonly used means,
- To eliminate any infiltration risk from acid effluents or the refractory and the blocking of mobile grids (coal boilers),
- To neutralize correctly and protect the heat exchangers during long stoppages.
|
 | THE PROBLEM'S DATAS | |
In the above-mentioned generators, the deposits clogging the heat -exchangers are mostly made of : |
| Ever since boilers were made, running or pressurized water has been and still is the most commonly used way to clean off-load boilers.
The amounts of water used are proportional to the volume, hardness, adherence and acidity of the deposits, as well as in some cases the difficult access to the gas course.
Only exceptionally are boilers designed to be washed with water. In spite of all necessary precautions (covered grounds and grids, sealing with foam or cast plaster), infiltration of acidified water is often seen between the pipes and the casing of the boilers.
Acid corrosion can then develop very quickly and sneakily, because it is invisible, and provoke very serious damage.
Ever since 1992, polluted effluents generated by water-cleaning must be collected and treated before their disposal in a specialized unit. These operations make cleaning more costly.
It is also a commonly accepted opinion that water cleaning is not "a walk in the park" for those in charge of it.
|
 | THE SOLUTION | |
Caring about the protection of the heat-producing equipment, the environment and staff comfort, AIT DRIVEX has developed a semi-dry cleaning process combining : - a scaling product with a strong soaking and neutralizing capacity,
- an original application method where the product is applied as foam,
- A tube-cleaning method: organic sanding with the help of vegetal products.
|
| Since the product is able to rapidly penetrate inside the deposits while at the same time neutralizing their acidity, the quantity of product is minimal, the dampening risks are eliminated. Finally, water-cleaning is unnecessary, and would even be harmful to the preservation of the heat exchangers.
The necessary quantity of product depends on : - the amount of deposits to treat,
- their acidity: pHcount.
Generally, a few dozen liters of the product are enough for boiler treatment.
Photo: foam projection. Projection of foam on pipes needing treatment.
|
 | THE ADVANTAGES OF FOAM | |
The use of these products as foam has a number of advantages : - foam does not leak, which means that infiltration risks are eliminated,
- foam clings longer to deposits, which means that less product is needed to treat equal amounts of deposits
- foam fills all existing volumes: all heat-exchangers are treated,
- foam does not evaporate when in contact with hot surfaces: it is possible to start the treatment as soon as the temperature is bearable. In smoke-tube boilers, treatment can be started as soon as the metal's skin temperature is below 70°C,
- oam does not generate any effluents.
|
|
|
 | THE ADVANTAGES OF ORGANIC SANDING | |
Organic sanding made with abrasive products of a vegetal origin : - cleans as efficiently as sanding with a product of a mineral origin but does not present any kind of risk for the metal skin of the pipes,
- is eliminated by aspirator, saving time and man-hours,
- absorbs the humidity from the deposits
- can be destroyed at a lesser cost in specialized units
|
 | APPLICATION OF THE PRODUCT AS A FOAM | |
|
 | RESULTS | |
A heater cluster (heavy fuel boiler) BEFORE/AFTER.
The upper part of the lower tank from the same boiler after treatment.
|
LA CORROSION ACIDE BASSE TEMPERATURE
En brûlant, le soufre du combustible (fuel lourd ou résiduaire et certains charbons) donne naissance à de l'anhydride sulfureux (SO2). Mis en présence de l'oxygène de l'air en excès, dans le cas de combustion oxydante ou oxydo-réductrice, et de catalyseurs de conversion tels que le vanadium, le fer ou le nickel, une partie du SO2 formé se transforme en anhydride sulfurique (SO3).
Dans certaines conditions de température de peau du métal et d'hygrométrie, le SO3 se condense et forme de l'acide sulfurique (H2SO4).
On se souviendra enfin que le SO3 est retenu en adsorption par les imbrûlés carbone. La destruction en continu des imbrûlés carbone par oxydation peut être obtenue par l'utilisation de l'un des procédés de Traitement Chimique Préventif de la gamme DRIVEX 2000.
|
|
 |
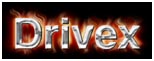 |
|