An explanation to the phenomena of fireside clogging and low temperature acid corrosion in boilers. Overview of the cleaning means on-load and off-load, their advantages and setbacks.
Presentation of three efficient off-load cleaning processes: foam chemical cleaning, soot-removal with self-propelled sweeping, low pressure steam chemical cleaning.
Clogging is expensive. According to figures published by GRETH in 1990, clogging in steam or superheated boilers has a cost of 50 Million euro to French economy each year, not to mention the output losses generated by stoppages due to drops in thermal production, cleaning or corroded pipe replacement.
MAIN REASONS FOR CLOGGING
1/ Fuels
In the past 20 years, fuels, solid or liquid, have changed. Heavy fuels are the product of elaborate mixes. French coals, not very ashy or sulfured, are increasingly replaced by imported coals, which, although controlled are sometimes harder to burn and come from multiple origins.
2/ Savings
It has been tried, sometimes successfully, to reduce the weight and bulk of boilers, while keeping the same output, in reducing the smoke flow sections and multiplying the chicanes placed on the gas course. This led to an increased loss of production, but also, alas, to soot deposits in the areas less licked by the flame (bends and angles for instance).
3/ Boiler automation
Automated running has removed trained, experienced personnel, who could evaluate a fire by simply looking at it, away from the boilers. Their handling depends more than ever on the measuring and testing instruments, hence of their maintenance and regular gauging.
4/ Longer stoking campaigns
For similar economical reasons, the length of the stoking campaigns was improved. Statutory visits, hence cleaning, are normally made every 12 or 18 months, but derogations up to 40 months are given to some industries (oil and petrochemistry for instance).How can one control clogging on heat exchangers over periods that long when it is possible that it may brutally and irreversibly increase in a matter of days ?
5/ The ageing process of boilers
According to a study published by the end of 1994 by a controlling body, 62 % of existing boilers are over 20 years old. Would it be safe to assume that these boilers are still as efficient, if one considers their clogging for instance? Apart from totally stripping them down during each cleaning, which would be expensive, it is unavoidable that parts difficult to reach would progressively become clogged.
ON LOAD CLEANING MEANS
There are a number of solutions to try and keep up or get back the performances of these generators, each one of them has its pros and cons.
1/ Steam or air-compressed soot removal
These processes demand special equipment adapted to boiler or heat-exchanger technology on which they are installed. They must be used according to the maker's prescriptions: steam specifications, air pressure, use frequency…Besides, they need a regular maintenance, sometimes expensive. Because of their limited range, there are several of them and their cost adds up: specialized pipes, taps, access bridges, lagging, compressors… Besides, the smaller the boiler, the more effect the steam soot removal intake will have on the downstream process, or even on the running of the generator itself.
However, this technique is the only one with a proven record, whatever fuel is in use (viscous, powdery).
2/ Striking
It is reserved for small power boilers made to that effect and subjected to powdery clogging. Its possible noxiousness on collectors and pipe supports is not really known. Furthermore, clogging speed being difficult to forecast, it is uneasy to establish a production planning.
3/ Shot blasting
This technique, that destroys the oxide layer covering the pipes, must be avoided when skin temperature is above 450°C and is not applicable to boilers above 50 t/h, except locally (economizers or air heaters for instance). Besides, accidental dampening of the ashes can provoke serious clogging, hard to eliminate.
4/ Acoustic vibrations
Preventive and non-curative technique as in the others above, it has the advantage of not being aggressive to the heat-exchangers. It is efficient on non-viscous ashes and it can be associated with a chemical or mechanical process when temperatures are over the fusion point of the deposits.
5/ Injecting chemical reagents in the fuel
Fuel additivation is only conceivable for liquid fuels. Globally, if reagents are carefully chosen, results are satisfying.
Adding liquid or solid reagents to coals or waste (industrial or domestic), is a major problem when trying to get a constant ratio between the chemical reagent and gas or deposit. A reagent injected in fuel cannot, unless it is that elusive universal product we are still all waiting for, have a behavior adapted to any local situation. At best it will be inefficient, at worse, it will have harmful side-effects (eggshell for instance).
Besides, some powder reagents have a very low fusion point. This means they can melt in the waste heating-zone or in the coal hearth-cavity and then become totally inefficient. Finally, some compositions are easily flammable.
6/ Injecting chemical reagents in the flame
Liquid chemical reagents injected in the flame or in the flue gas are far more efficient, easier to use, and, above all, can be used with any kind of fuel, solid or liquid.
Some of the products only have an instant and/or local action, for instance on slag. This means they ought to be permanently injected in the furnace.
Others, more numerous, have a film-forming effect. The active principles they release fix themselves on the heat-exchangers and react locally to the existing deposits or those to come. As they self-destruct in action, they can neither initiate nor increase clogging. Their lifespan in the pipes is such that a periodic injection is enough.
Causes for failure are mostly due to a poor choice in reagent, its bad pulverization in the flue gas due to preferential flows or a product loss between the injection point and the surfaces being cleaned.
Finally, experience shows that, except for a few exceptions, chemical treatment still needs mechanical soot removal. They are still necessary to remove crumbly deposits, but it does make their use sparser, which means more energy savings and less polluting emanations. Mechanical processes described above and chemical processes therefore work together, not against each other.
In fact, there is no miracle or standard solution. Each case is a particular one and must be studied beforehand to clearly define the goals to reach and the means for it. Unless they understand this need, constructors, product-makers and users face unavoidable disillusion.
LOW TEMPERATURE ACID CORROSION
All heat-generators running on fuel-oil (heavy, domestic or residuary) and coal are exposed to low temperature acid corrosion as soon as the fuel they use fractions of a percent of sulfur or chlorine and that a certain number of conditions are met.
It is during long-term stoppages that corrosion is most intense but it can develop even on-load. As soon as metal-skin temperatures are close or below acid dew point (110 to 150 °C according to their sulfuric count) which is the case with hot water boilers (T= 110°C) or generators running only part of the day or the wee
Night or week-end stoppages, leaks to the steam soot-removal systems, water in the soot-removal air, unwanted air intakes, especially in depression-boilers, return water temperature too low, are as many reasons to find these two parameters together. Acid then attacks metal, which turns to ferrous sulfates, then the ferric and so on until there isn't any metal left at all.
Traditionally, cleanings are made with running water or water under pressure, for simple reasons: water dissolves sulfates and vanado-sodic deposits, infiltrates between the pipes and the refractories, between the pipes and the casing, all different parts with difficult access unless one decides to dismantle the whole machinery when cleaning.
Corrosion, sly because invisible, will settle in these areas and work on the metal of the pipes and refractories even after the generator is back in use. And contrarily to given ideas, the addition of a small percentage of neutralizing product diluted in the cleaning water will not be enough to eliminate all acid traces and dry the refractories.
Cleaning generators is part of the workload that can be subcontracted to professionals using tried methods. In the medium or long run, neutralization and complete wash-up of the heat-exchangers on the fireside will improve performances and extend the generator's life. These operations must be considered as a form of preventive maintenance.
INNOVATIONS IN OFF-LOAD CLEANING
In recent years, a few innovating companies have been working on optimizing the cleaning of the heat-exchangers on the fireside, improving at the same time staff working conditions, preserving generators and reducing effluent production, which, legally, must be destroyed in specialized units.
1/ Foam chemical cleaning
One of these innovating processes, named CECONET, consists in replacing, each time it is possible, water with a chemical product better adapted to the nature of the deposits to eliminate and applied as foam to reduce infiltration risks between the pipes and the refractories and collect less humid effluents.
Experience has taught us that foam :
- does not stream and clings longer to the deposits;
- can fill a very large volume from a small amount of product;
- has a better resistance to heat allowing to work on surfaces still hot;
- does not generate more effluents than there are deposits in the boiler, and, reacting to the deposit, the product will destructure it, immediately neutralizing acidity and combining with them;
- gives better working conditions for the personnel than water: no splashes, no other protection needed than gloves and goggles.
Used quantities are very small (400 liters for a 70 MW boiler for instance). The aqueous support evaporating quickly, there are only dry deposits left, easy to eliminate with an aspirator. Organic sanding will strip the tubes and not increase notably the volume of effluents (600 liters for the boiler mentioned above).
The liquid product is then transformed in foam with special equipment, working without the usual tank under pressure, hence lighter and easier to move, able to produce a great amount of foam in very little time (800 l/h in continuous mode).
The quick application of foam and small quantities of product make it possible to repeat several times a passage over clogged areas without making the operation longer.
In any case, the quantity of dry effluents is lesser than that of the liquid ones generated with water. Their destruction in a specialized center will also be less expensive.
Foam chemical cleaning suits brick generators running on heavy or residuary fuel and coal, but also smoke-tube boilers. Combustion chamber, convecting clusters, water economizers and metallic air-heaters are regularly cleaned this way. In some cases, for instance in economizers with notched fins, organic sanding will be replaced with a more efficient hydraulic cleaning. As all deposits will have been scaled and neutralized beforehand with the chemical treatment, the hydraulic cleaning will be shorter and the volume of effluents reduced by more than half.
Foam chemical cleaning has already convinced a number of boiler users either with superheated water (urban heating) or steam (industrial use) AND HAS BEEN APPROVED BY CONSTRUCTORS AS WELL AS CONTROL AUTHORITIES; Plant generators in Caen, Pontoise, Vitry-sur-Seine, Calais, Massy, Bobigny, Diddenheim have been cleaned in this way for more than two years.
2/ Soot removal with internal sweeping
The second process, named "FERRET" is meant for soot-removal in smoke-tube boilers. It is a machine equipped with an internal self-propelled sweeping system, with a pneumatic engine integrated in the body of the machine itself, and not a rotating tool as are its rivals.
The machines moves autonomously inside the pipe, no more need to push or pull on the hose which, in the other machines, sends the rotating movement from an outside motor. The machine is positioned, equipped with a brush the same diameter as the pipe, at the starting end of the pipe, then, the air valve is opened with a foot pedal. Once at the other end of the pipe, the machine will stop for lack of a solid place to stand on, a slight tug on the air-hose is enough to make it come back to the operator. This hose goes through a Y-shaped tubular joint; the second branch is connected to an aspirator.
The FERRET System can be used to clean smoke passages in any section (circular, square, etc…) whatever their length. The shape of the brush ant the length of the hose will be the only changes needed. In a boiler normally clogged, a return trip inside a 6 meters long pipe needs less than a minute.
3/ Low pressure steam chemical cleaning
Much better known, the third process, named "NEUTROL" has proven itself for over 20 years. It is a happy compromise between water cleaning and dry sweeping, not very efficient, being only limited to surfaces with an easy access. It is also complementary to the CECONET process, notably for cleaning the super heater clusters in heavy fuel boilers, very often clogged up by large and sticky vanado-dodic deposits.
It consists in an injection inside cold boilers and furnaces of a mix of low pressure steam and scaling as well as neutralizing chemicals. During the operation, the register is kept wide open, or the extraction fan is switched on at a small speed, allowing the steam to follow the gas flow and reach the farthest heat-exchangers. It is done one heat-exchanger after the other: super heater cluster, then convection cluster, then if any, air-heater.
Its action is twofold :
- A chemical action: soaking and neutralizing agents lead to a sediment scaling and acid neutralization. At the beginning, the product pH is from 12 to 13.
- A physical action: steam softens the deposits, which makes their removal easier thanks to jet pressure.
A pH permanent control for the effluents, collected to be treated later, will allow calculating the necessary amount of product. Humidification being cut down to a minimum, restarting of the generator will allow a swift drying.
NEUTROL has proven itself on all kinds of generators using all kinds of fuels, fossil or residuary. Two recent examples illustrate the extent of its applications.
Near Grenoble, in a recovery boiler installed downstream an incineration furnace for chlorined waste, very sticky and hard deposits were only eliminated with this process, the finishing being done by sanding.
In Greece, in an electric plant, a 150 MW steam generator was previously dry cleaned by subcontractors, with bars and brushes. One can imagine the results.
Steam chemical cleaning made it possible to restore a state of cleanliness unseen for years to the heat exchangers by eliminating a few dozen tons of carbon and vanado-sodic deposits. The operating time was drastically reduced.
CONCLUSION
An extensive cleaning and neutralization, made by trained personnel using efficient processes :
- make a preventive action cheaper than it seems;
- will keep generators operational safer and longer slowing down their ageing and save fuel;
- contribute to stay within present regulations in matters of waste and reduce their elimination cost.
|
|
 |
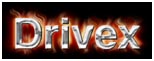 |
|